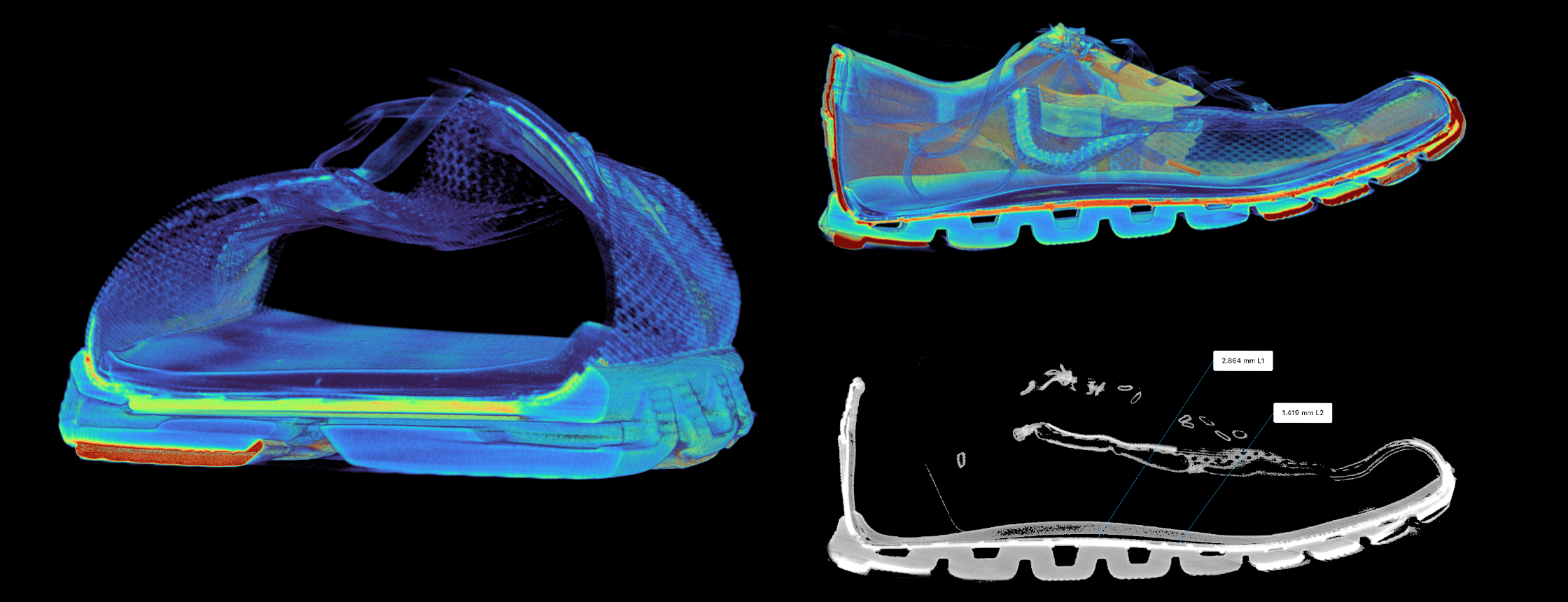
A popular global footwear and apparel retailer turned to Lumafield to streamline their PPAP.
Summary
- The Production Part Approval Process (PPAP) is an extensive and often lengthy quality assurance framework designed to ensure new parts and manufacturing processes meet customer specifications before large-scale production.
- After decades of reliance on destructive testing as part of their PPAP process, a popular global footwear and apparel retailer turned to Lumafield’s Neptune industrial CT scanner to reduce the time and labor required.
- The company’s line of products includes specialized equipment like metal spiked track shoes, which had proven challenging to examine due to the density of the spikes.
- With Voyager, the company can more effectively analyze both their own shoe designs and their competitors’ shoes as part of the development process.
Background
For over 75 years, our customer has been developing performance footwear known globally for setting the highest standard of comfort and quality. They are a major player in one of the most competitive segments of the retail market, a position requiring a fierce commitment to quality control. In today’s shoe market, any inconsistencies in quality that lead to product failure in the field can be damaging for this customer’s brand.
Design iterations 80% faster
The customer’s Production Part Approval Process (PPAP) has historically been a lengthy and labor intensive one, with engineers heavily reliant on destructive testing to examine the integrity of the inner structures and bonding materials in their shoes. It’s not just their own shoes that our customer was cutting up; a critical part of their product development process involves closely examining competitors’ products. The obvious benefit of examining rival footwear is for research and development purposes, but it also comes with a legal benefit. Closely inspecting products from other brands helps this customer ensure that any new technology they develop does not infringe on existing patents.
As technology in the footwear industry continues to push the limits of performance, manufacturers need to incorporate actionable data into a more efficient production process. Examining the inner workings of their shoes has long been an essential but labor-intensive process which limits the ability of the company’s employees to work collaboratively across the development cycle.
Seeking efficiency and sustainability gains, the company invested in Lumafield’s industrial CT scanning technology. This non-destructive method creates detailed 3D images of the shoe's interior, allowing for virtual inspection of seams, adhesive integrity, and material quality without compromising the product. Their decision was spurred by a referral from an executive at a direct competitor who had already adopted Lumafield’s Industrial CT platform and had seen significant benefits.
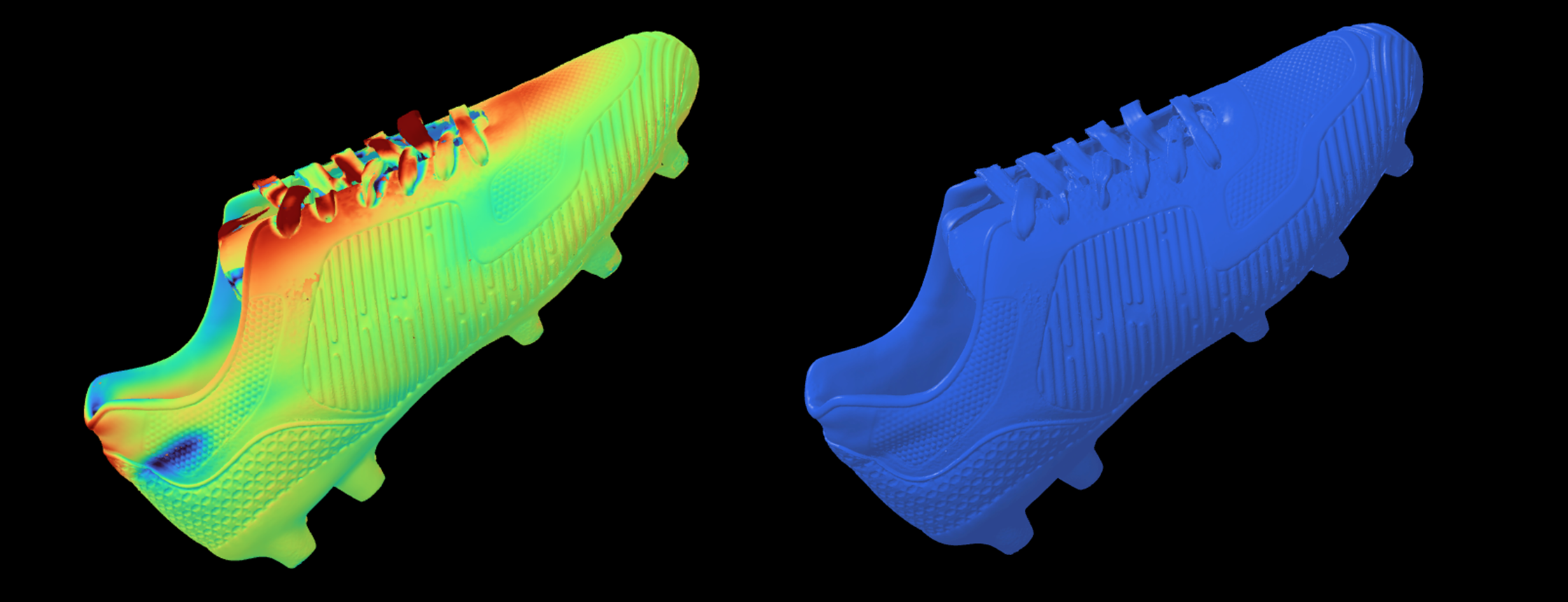
The ability to virtually “slice” through the shoe using Lumafield's browser-based Voyager analysis software has been a game-changer for the company’s PPAP. Design iterations now happen 80% faster, as adjustments can be made based on digital analysis without waiting for new physical prototypes. Material waste has plummeted, as fewer physical samples are used and ultimately destroyed. With Neptune enabling a more efficient and collaborative approval process, the risk of costly delays due to late-stage issues has been significantly reduced.
“CT scanning isn’t just creating a faster approval process. It’s about building a more responsible approach to manufacturing—minimizing waste from prototypes and maximizing the quality of every product we put out there,” said the company’s VP of Product Development.
Redefining Collaboration
For the top manufacturers, bringing a new footwear product to market is a process reliant on cross-functional collaboration on a massive scale. With their physical shoes now converted into immersive 3D scans, specialists from across the company can now easily contribute their unique knowledge to the product in real-time by leaving Comments and Bookmarks in Voyager—ensuring designs are optimized for performance, production, and market appeal.
We’re getting higher quality products to market more efficiently than ever before. Scanning products with Neptune has unlocked new levels of collaboration and allowed us to instantly bring key stakeholders around the world into the testing process.
— Senior Product Designer