Surface 3D scanners vs. industrial CT: what’s the best way to get an accurate surface scan?
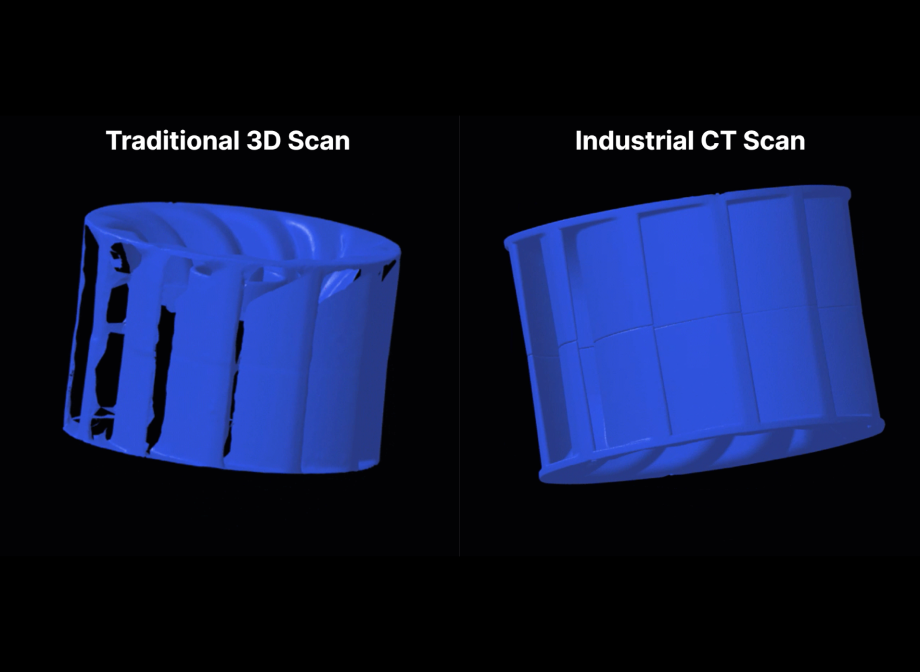
Surface 3D scanners vs. industrial CT: what’s the best way to get an accurate surface scan?
Engineers who want to capture digital models of their parts have a wide range of options, from free smartphone apps to laboratory instruments that cost over $1 million. In this article, we’ll compare scanners that use lasers or visible light to capture the surface of an object to scanners that use X-rays to capture a full model of an object’s internal and external features.
As you can see from the comparison below, 3D scanners and industrial CT scanners are both capable of producing accurate mesh models of an object's surface, but they differ in their ability to capture features that are not superficially visible on the part, like areas that are hidden by overhanging geometries.
Lumafield’s Voyager software can visualize, analyze, and share 3D scans from either type of scanner. It’s equipped with an AI co-pilot that can answer complex engineering questions and guide you through analyses, and you can get started with Voyager for free.
Surface scanners
3D surface scanners are available at a wide range of price points using several different technologies:
- Free or freemium smartphone apps like Polycam, Scaniverse, Kiri Engine, and MagiScan. These use a combination of photogrammetry (comparing images from different angles to determine 3D geometry) and LiDAR (on phones that are equipped with Light Detection and Ranging capabilities).
- Laser scanners that move a laser beam back and forth across an object and measure the time it takes for the beam’s reflection to bounce back. Laser scanners from companies like Zeiss, Leica, Hexagon, and Nikon typically cost between $15,000 and $150,000 and may be configured for detailed industrial use or long-range applications in construction and mining.
- Structured light scanners project a known pattern of light across an object and analyze the pattern’s deformation to calculate the object’s shape. Professional-grade structured light scanners cost between $2,000 and $100,000. They may be configured as hand-held scanners that can move around an object (like those from Artec or Shining 3D), or stationary scanners that capture an object as it rotates on a turntable (like those from Keyence).
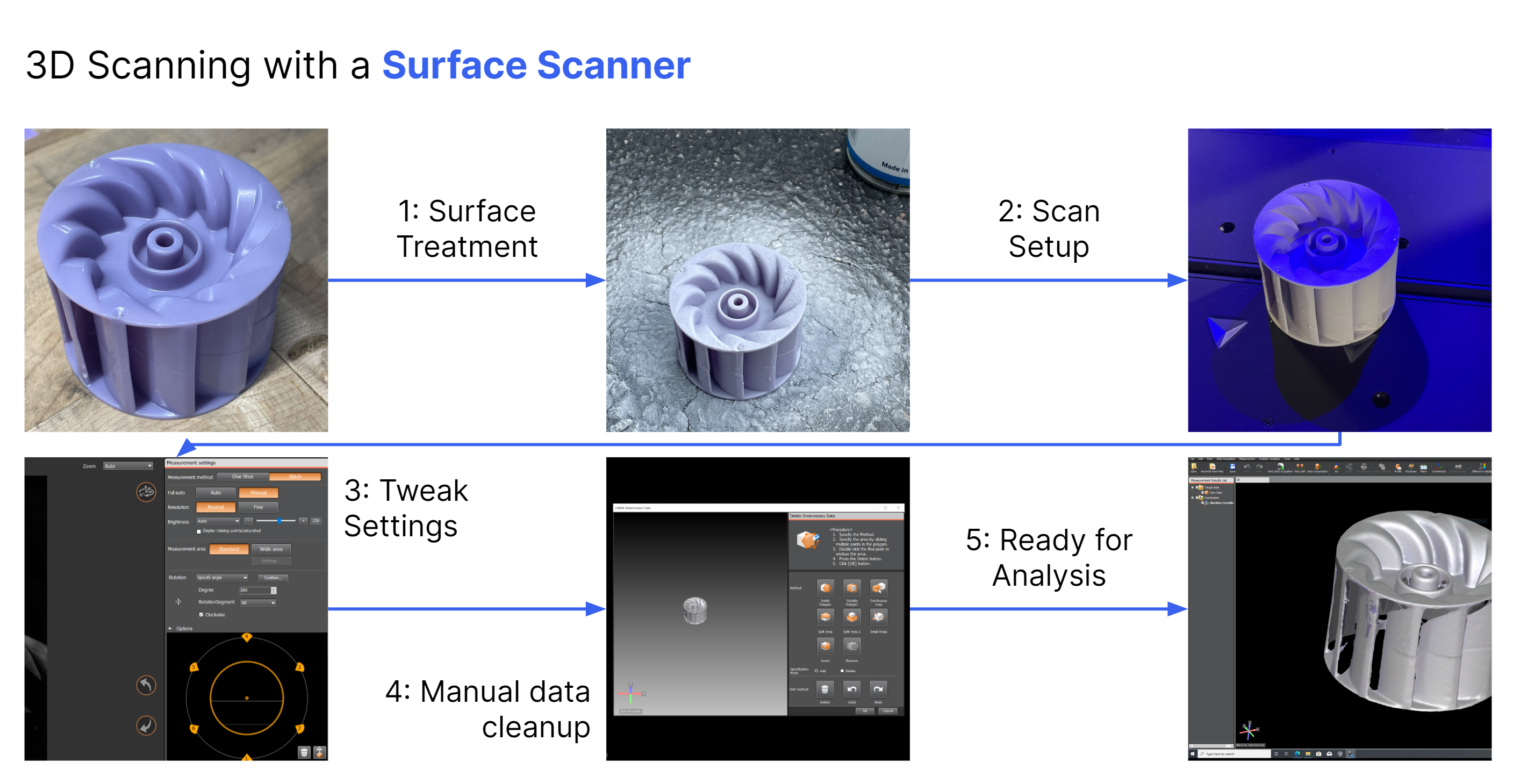
Surface scanners can capture accurate, high-quality 3D scans. Many surface scanners can even produce full-color models. However, surface scanners have two significant drawbacks.
Surface scanners are limited to capturing features that are clearly visible on the outside of the part. They struggle to accurately capture the shape of holes, bores, and other negative surface features. They are also limited by overhangs; if you don’t have a clear, straight-line view toward a feature, a surface scanner won’t be able to capture it.
Surface scanners also require careful preparation of your part, practiced scanning technique, and highly involved post-production. Reflective surfaces are difficult for surface scanners to read, so they must be prepared with a matte spray before scanning. During scanning with a handheld scanner, the operator must move slowly and stay within a narrow distance range from the scan subject. And many parts will require multiple surface scans that must be re-assembled in software after the fact.
Industrial CT scanners
Industrial X-ray CT scanners like the Lumafield Neptune work by capturing X-ray images of a part from different angles, then reconstructing them into a 3D model. The result is a volumetric model rather than a simple surface model, and it captures both shape and material density information. From a volumetric model, it’s easy to generate a surface model that captures the contours of a part.
Because they use X-rays instead of visible light, industrial CT scanners can capture both internal and external features in a single scan. They’re able to “see” through overhangs and represent geometries that aren’t clearly visible on the outside of the object, like deep bores and slots. And by adding a camera array to our Neptune scanner, Lumafield’s Surface Capture technology complements the capabilities of industrial CT by integrating high-resolution visible light data into the 3D models generated by X-rays.
This dual approach not only captures both internal and external features with unparalleled accuracy but also overcomes the limitations of traditional surface scanners, such as difficulties with reflective surfaces and hidden geometries. By combining these technologies, Surface Capture provides a comprehensive and precise digital representation, making it ideal for applications in industries ranging from automotive to luxury goods, where both surface detail and internal structures are critical.

Until recently, industrial CT scanners were exotic, expensive devices that required dedicated technicians. Lumafield’s Neptune industrial CT scanner makes this game-changing technology available to any engineering team. This low-cost scanner is designed for an office or workshop environment, with an easy-to-use touchscreen interface and powerful cloud-based analysis software. It’s even equipped with an AI co-pilot called Atlas that can answer complex engineering questions and guide you through your analyses.
CT scanners are set-and-forget tools that require no special preparation: just place your part in the scanner and kick off an Auto Scan; once the scan is done, you’ll have a reconstructed model ready to go.
Want to explore industrial CT for your application? Get in touch with Lumafield for a consultation with a CT expert.