Inspecting FDM 3D prints with industrial CT
Introduction to FDM
Fused deposition modeling (FDM) is one of the earliest forms of 3D printing. FDM printers use one or more heated nozzles to melt and extrude thermoplastic filament, depositing it layer by layer to form a part. FDM printers are common in a wide range of applications, from hobbyist workshops to heavy industry.
As with all 3D printing processes, getting the best results from FDM requires some specialized design knowledge and an understanding of its limitations. An industrial X-ray CT scanner can quickly pinpoint invisible features in FDM prints, including some that can cause failures.
Explore this CT scan in Voyager by creating a free account.
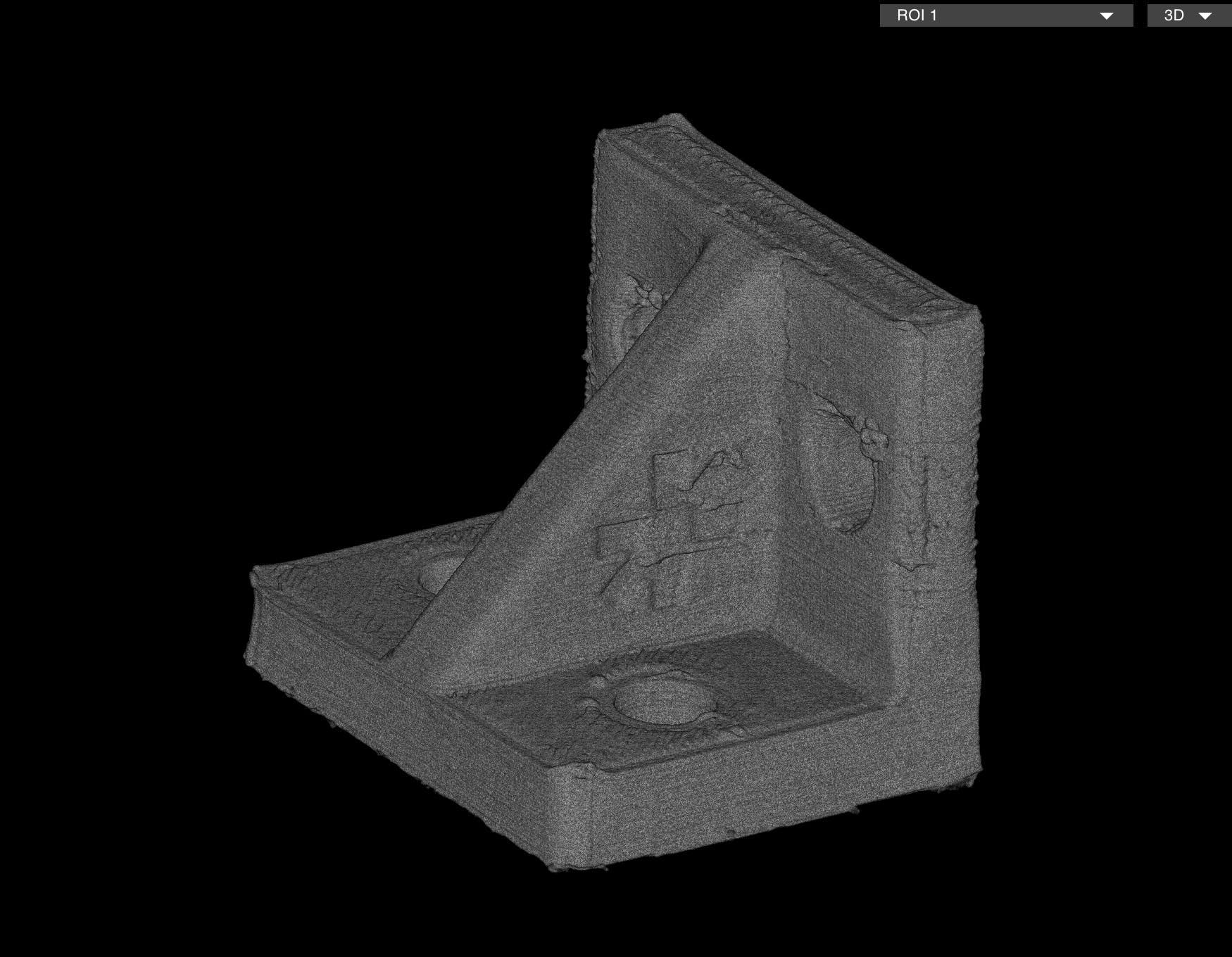
Internal supports
In order to save time and material, operators often configure FDM printers to fill large volumes with a sparse pattern. Here our CT scan reveals a honeycomb lattice inside the solid walls of the part.
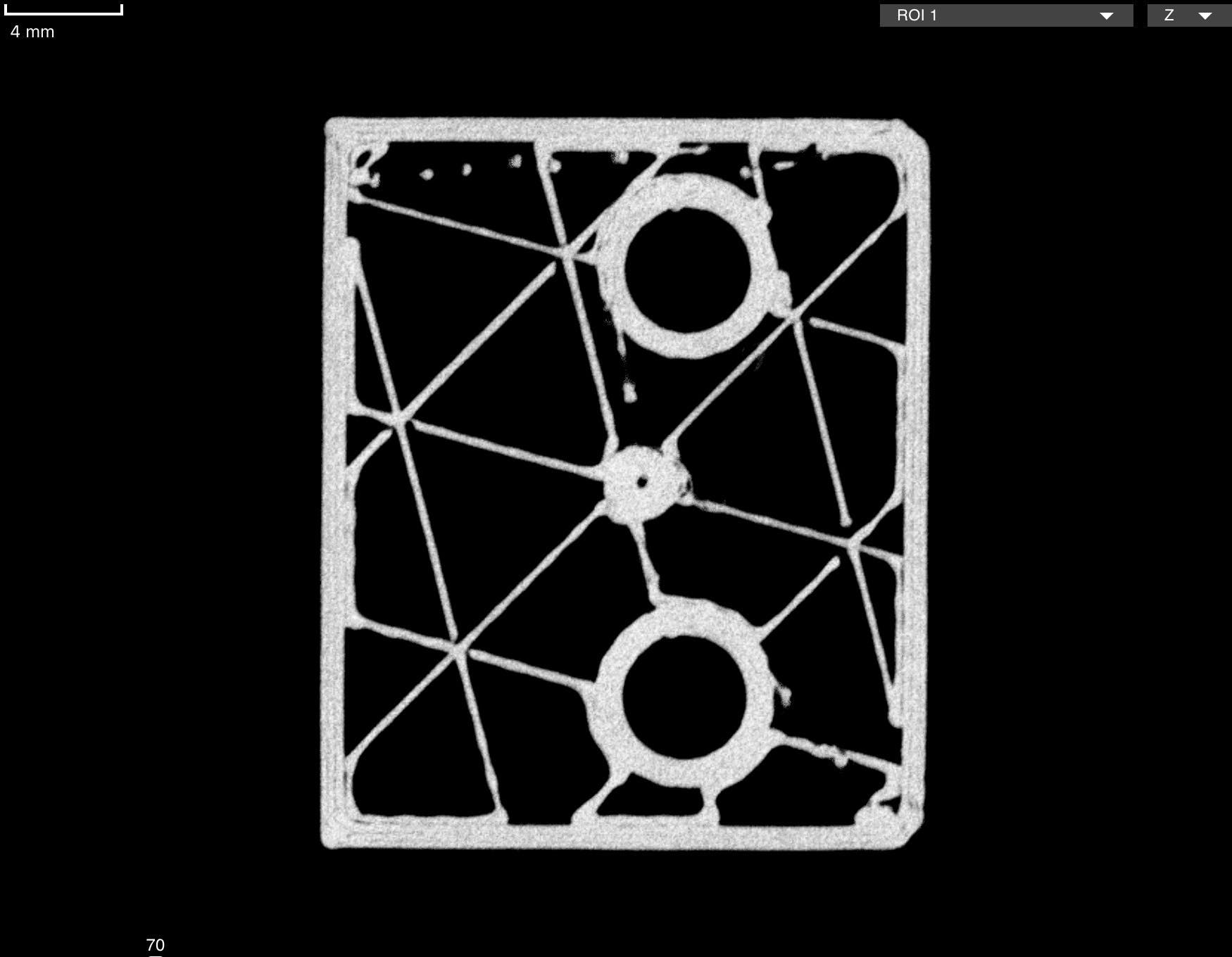
Layer quality
Cropping into our CT scan, we can see the unfused ends of the extruded beads deposited by the printer. Above the holes is evidence of insufficient support during printing: these layers are aesthetically rough, but they are also not fully adhered to each other, possibly creating a structural problem.
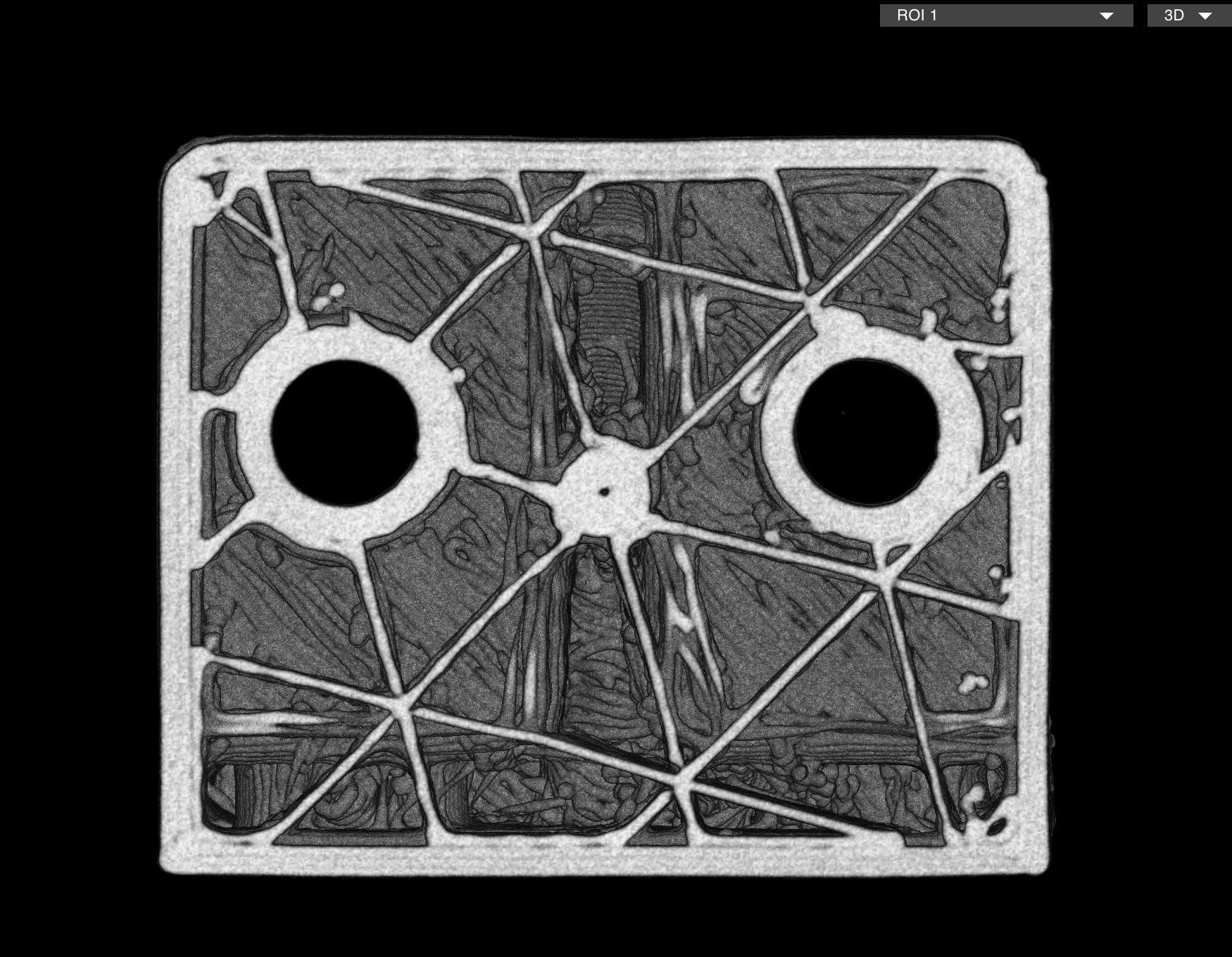
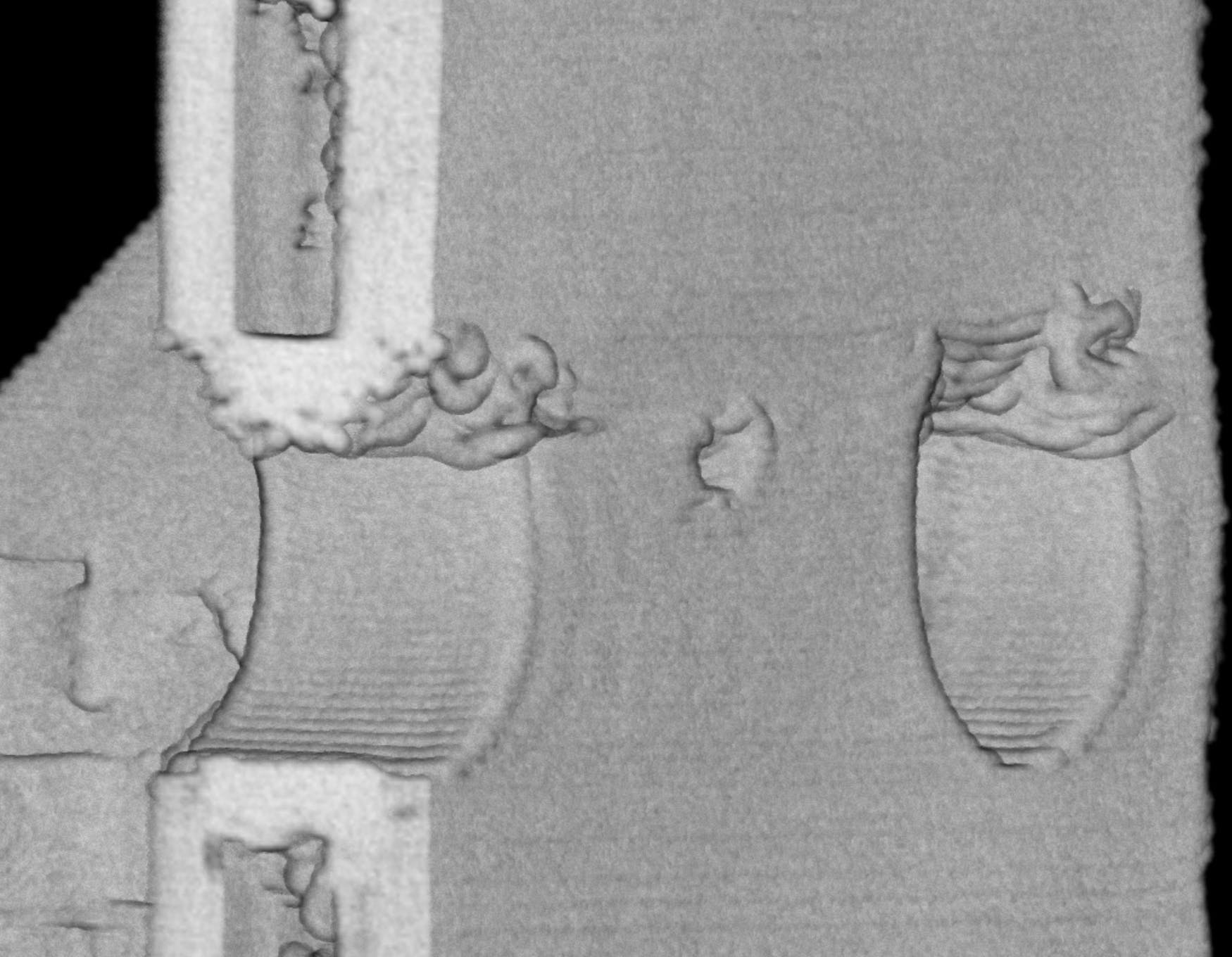
Internal features
This part was designed with a smooth channel 1 mm in diameter. The FDM printer created a significantly narrower channel with a rough profile—a problem that's outwardly invisible, but could render the part useless.
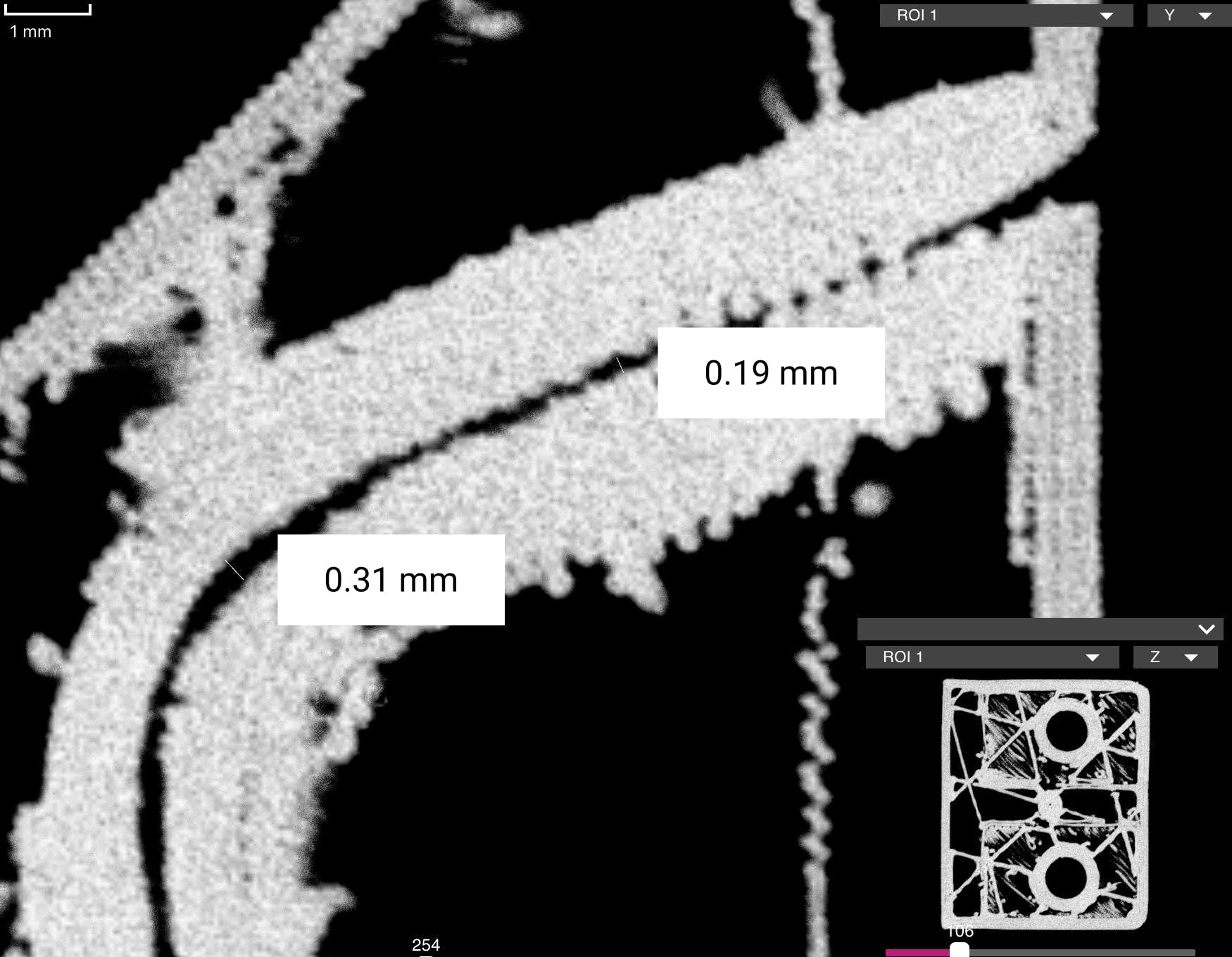
Other Articles in the Series
- Homepage: Inspect 3D printed parts with industrial CT
- Selective Laser Sintering (SLS)
- Stereolithography (SLA)
- Multi Jet Fusion (MJF)
- Direct Metal Laser Sintering (DMLS)