In our first scan with Lumafield, we saw what we were looking for. We saved ourselves four months.
Summary
- L’Oréal Group, a world leader in beauty products, has global initiatives around quality, safety, and sustainability. Project leaders in the company’s Packaging Qualification Labs uphold these through the entire lifecycle of the Group’s many products.
- Lumafield computed tomography (CT) empowers packaging engineers to qualify new designs and suppliers with confidence. L’Oréal’s engineers saved four months of development time by using Lumafield CT scans of a packaging prototype.
- Assemblies with multi-component seals are difficult for engineers to analyze. Conventional inspection methods, like cross-sectioning and using contact putty, are time-consuming and often do not provide the data engineers need. Within seconds of reviewing their first Lumafield CT scan, L’Oréal engineers found the evidence they had been searching for.
- L’Oréal uses CT scanning both in new product introductions and to continually improve mass production. Lumafield provides new data that gives the company’s engineers better insights across the product lifecycle.
Background
Consumers have trusted L’Oréal Group for over 100 years. Meeting customers’ requirements for performance and quality is an ongoing commitment for L’Oréal’s teams and a priority for the Group. Quality is a global commitment upheld by the entire company and all of the Group's brands worldwide.Guaranteeing packaging quality and safety is the goal of the Packaging and Development teams at L’Oréal. Product packaging is designed and approved in parallel with a product’s formula design, and the company tests formula stability, compatibility, ergonomics, and dispensing system functionality against the strictest applicable standards to guarantee the product's performance and consistent quality over time.
Seeing What Matters
In one recent case, a bottle and cap were leaking after inspection. Puzzlingly, the bottle’s individual components passed all traditional inspection measures. “We were trying to do dimensional analysis, but everything was within specification,” says Zach Mahoney, Director of the Packaging Qualification Lab.
In collaboration with Lumafield, Mahoney’s team obtained a CT scan of the assembly. “In our first scan with Lumafield, we saw what we were looking for,” Mahoney said. The culprit: a tiny 100-micron indentation inside the bottle's neck. Lumafield’s scanner provided the engineers with virtual slices that helped them inspect and measure the entire assembly in detail while keeping the seal in-situ and preserving all physical evidence.
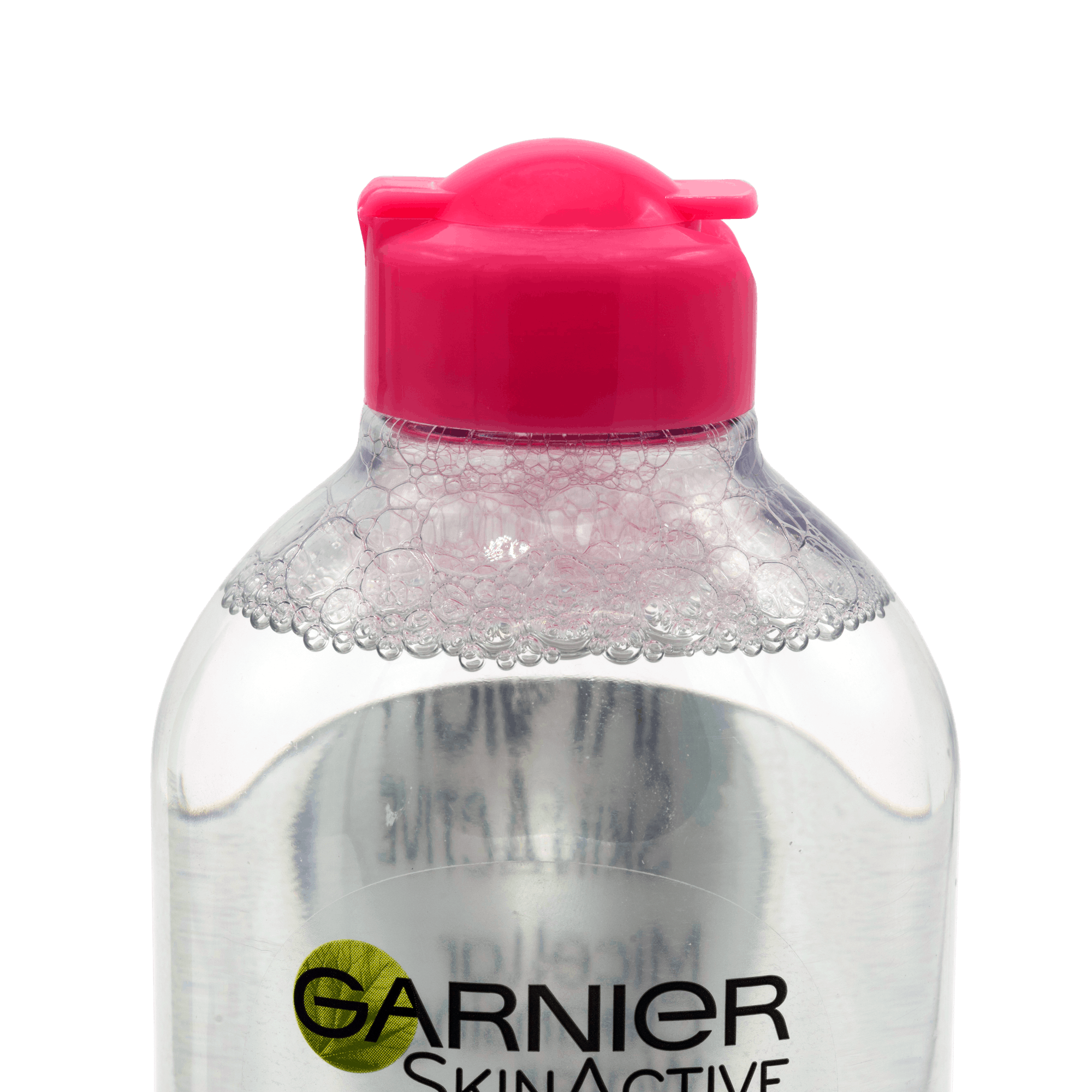
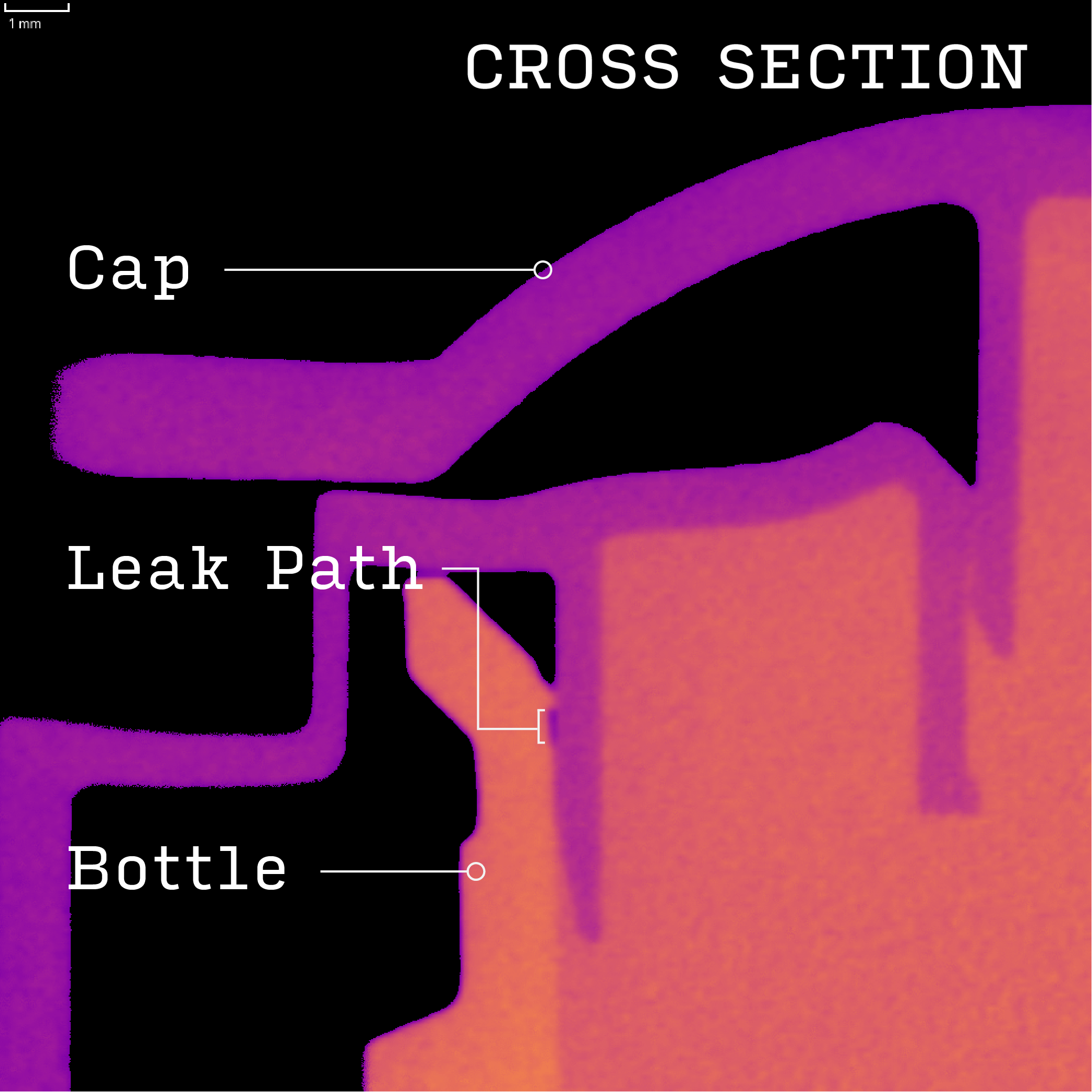
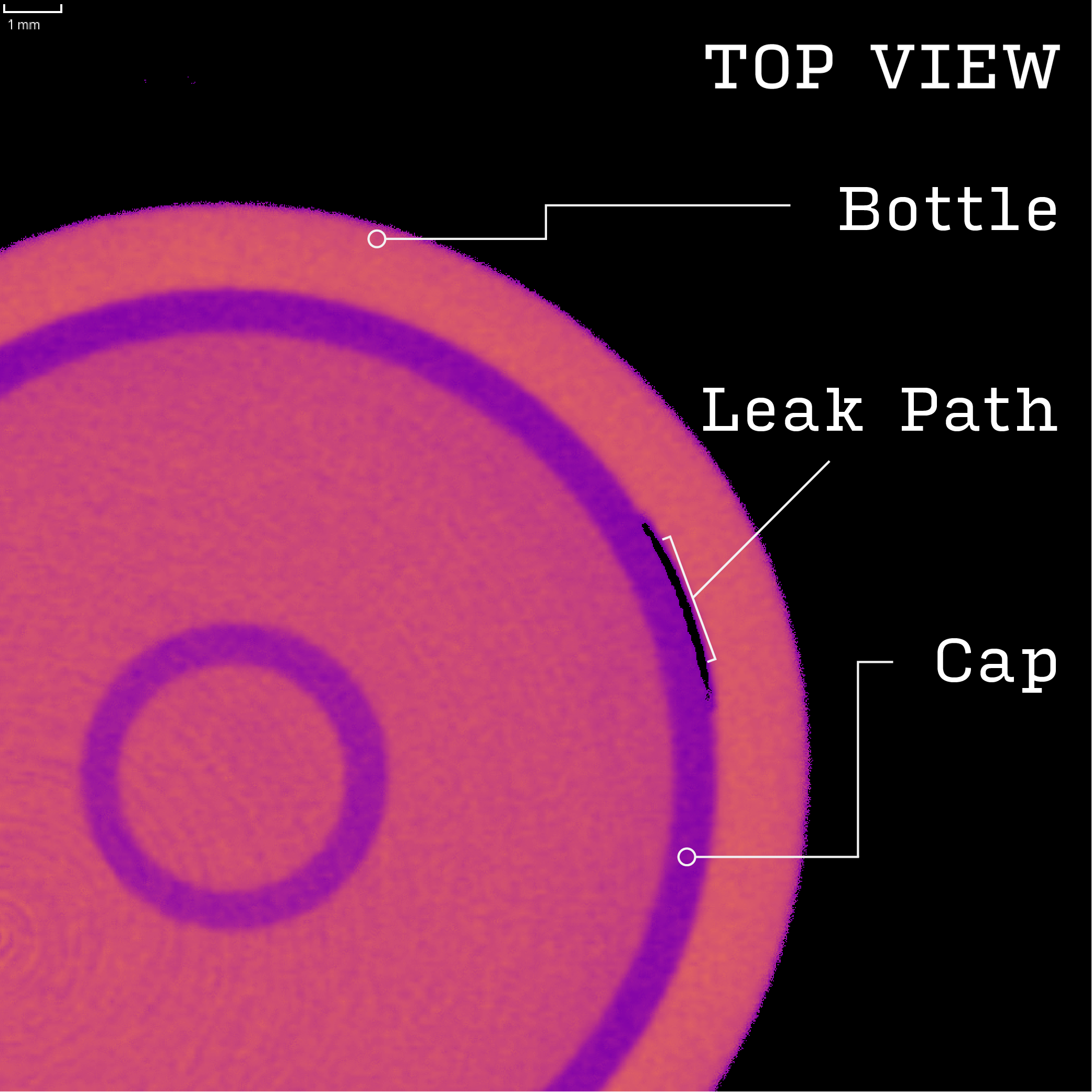
“If you are using a plug gauge, it’s never going to catch this,” Mahoney says. “If we had seen this CT scan first, we would have been able to skip all of that.”
Accelerating Development
During a different new product introduction, L'Oréal's engineers uncovered a multi-part interference using a Lumafield scan. “It became so simple. It was one of those instantaneous things,” says Mahoney.
The team used this information to iterate a new prototype instead of jumping to conclusions. “We said, before we just start making changes, let’s do a little study,” Mahoney said, and the team performed another scan. Lumafield’s rapid feedback gave the engineers confidence that they could resolve the issue quickly.
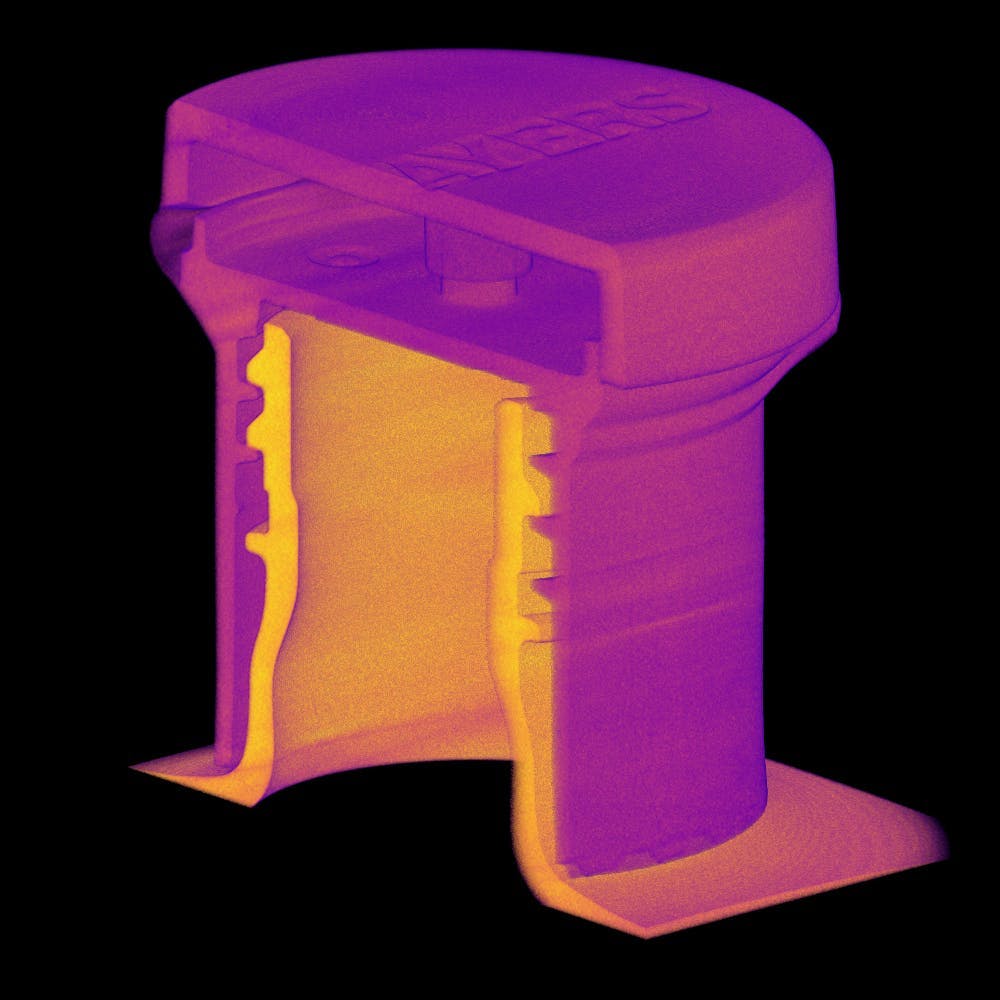
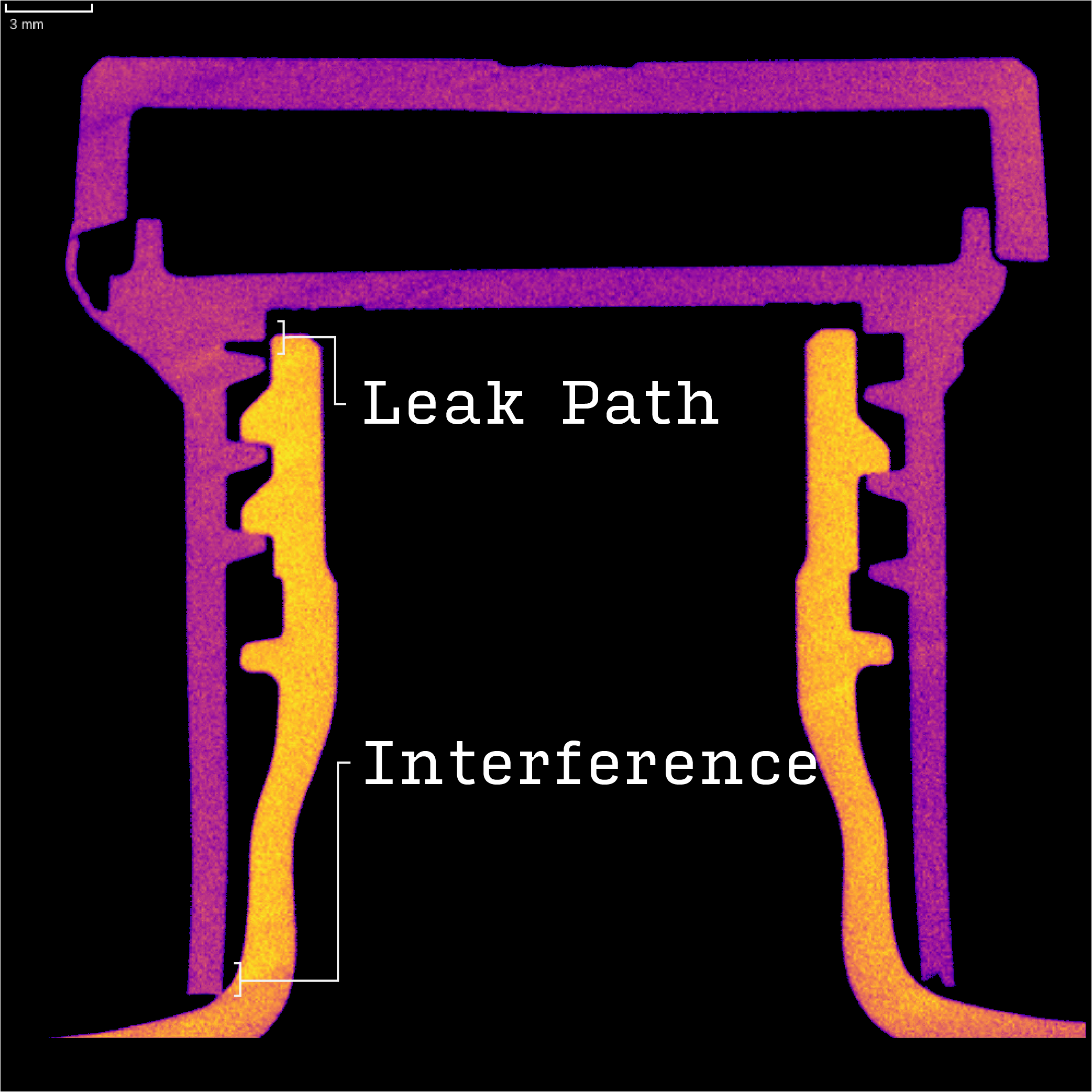
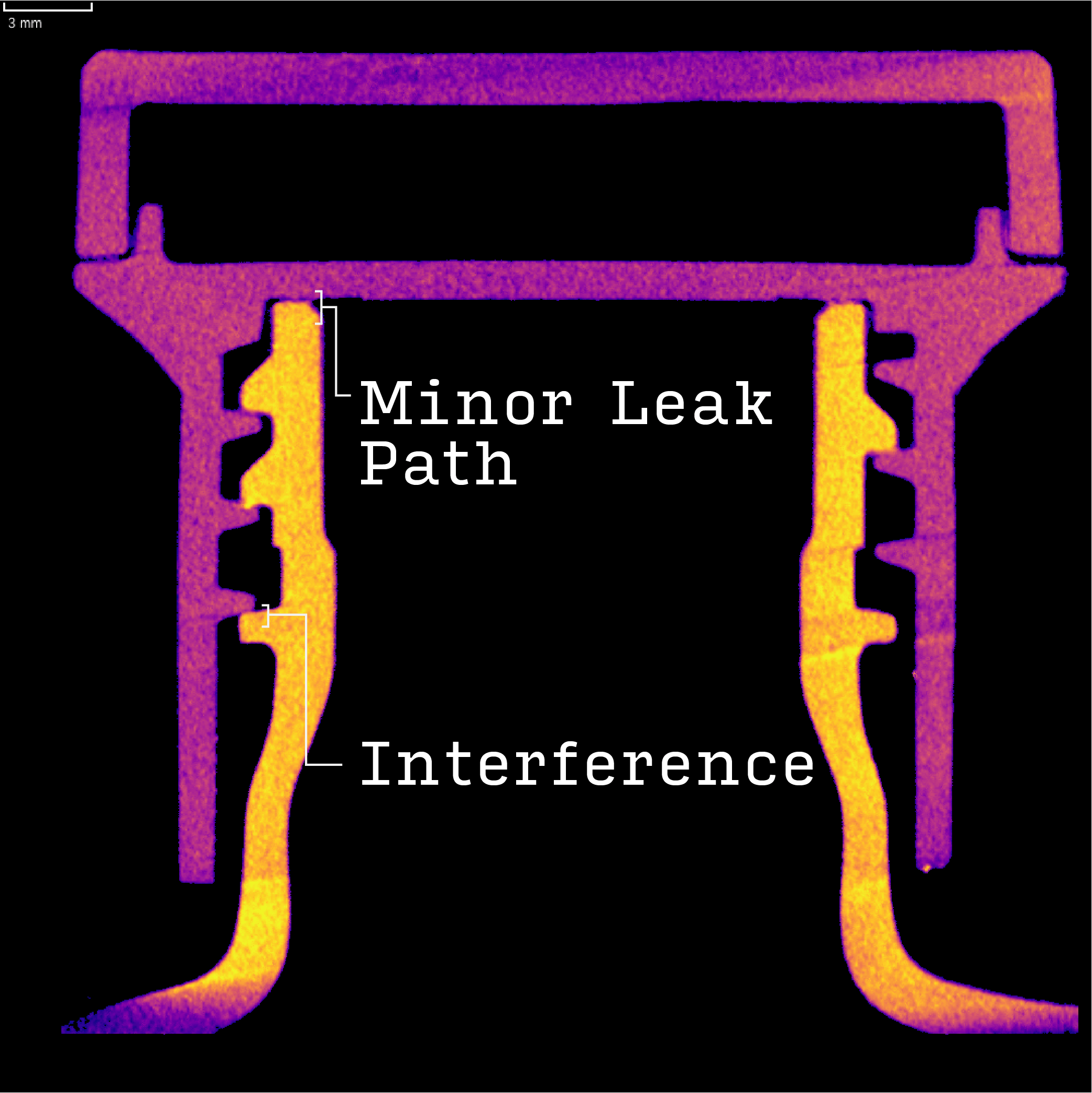
A Lumafield scan of a second prototype showed that the revised design was better but would require further work. “We saved ourselves four months of building a unit tool and then finding out that it was not good enough,” Mahoney says. “We’re starting to identify opportunities where we anticipate more.”
Data-Driven Decisions
While L’Oréal maintains a very high bar for product quality, the company also works hard to prevent service interruptions at its manufacturing facilities. In order to keep production running, L'Oréal's operations team must smoothly bring on new suppliers and replace end-of-life production tools. To qualify these sustaining efforts, Mahoney’s team performs accelerated-lifetime tests and other analyses to ensure that new suppliers and tools meet requirements.
During one recent qualification case, the lab found that caps from a new supplier performed differently compared to older caps during an aging test. The team turned to Lumafield’s scanner to understand the difference between the batches.
“We finally saw inside the parts. We started seeing air pockets in new parts where we didn’t see them in our older samples,” Mahoney says. The quantifiable data provided Mahoney’s lab the ability to uncover process variation that, if unchecked, could degrade the quality of the product.
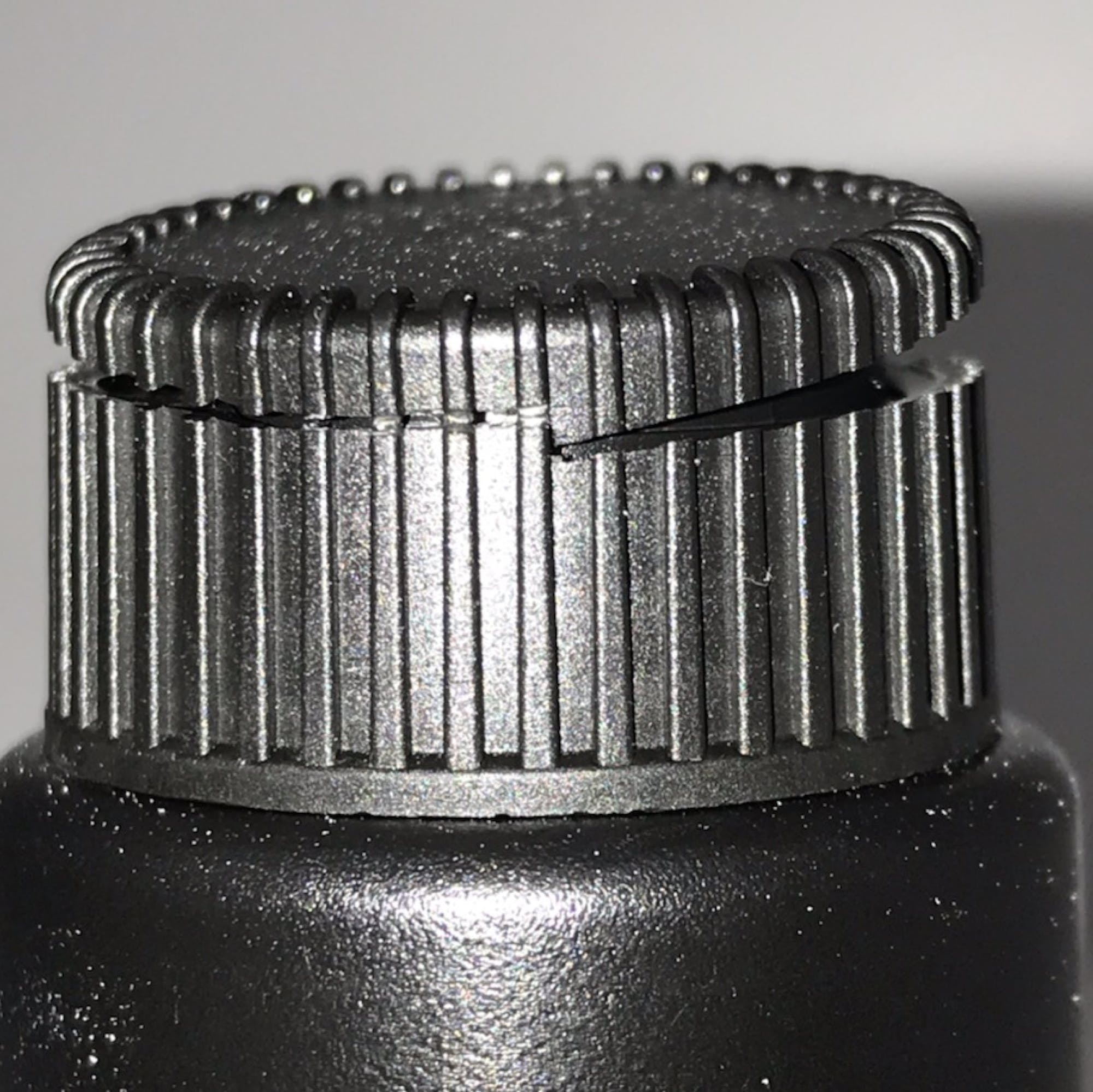
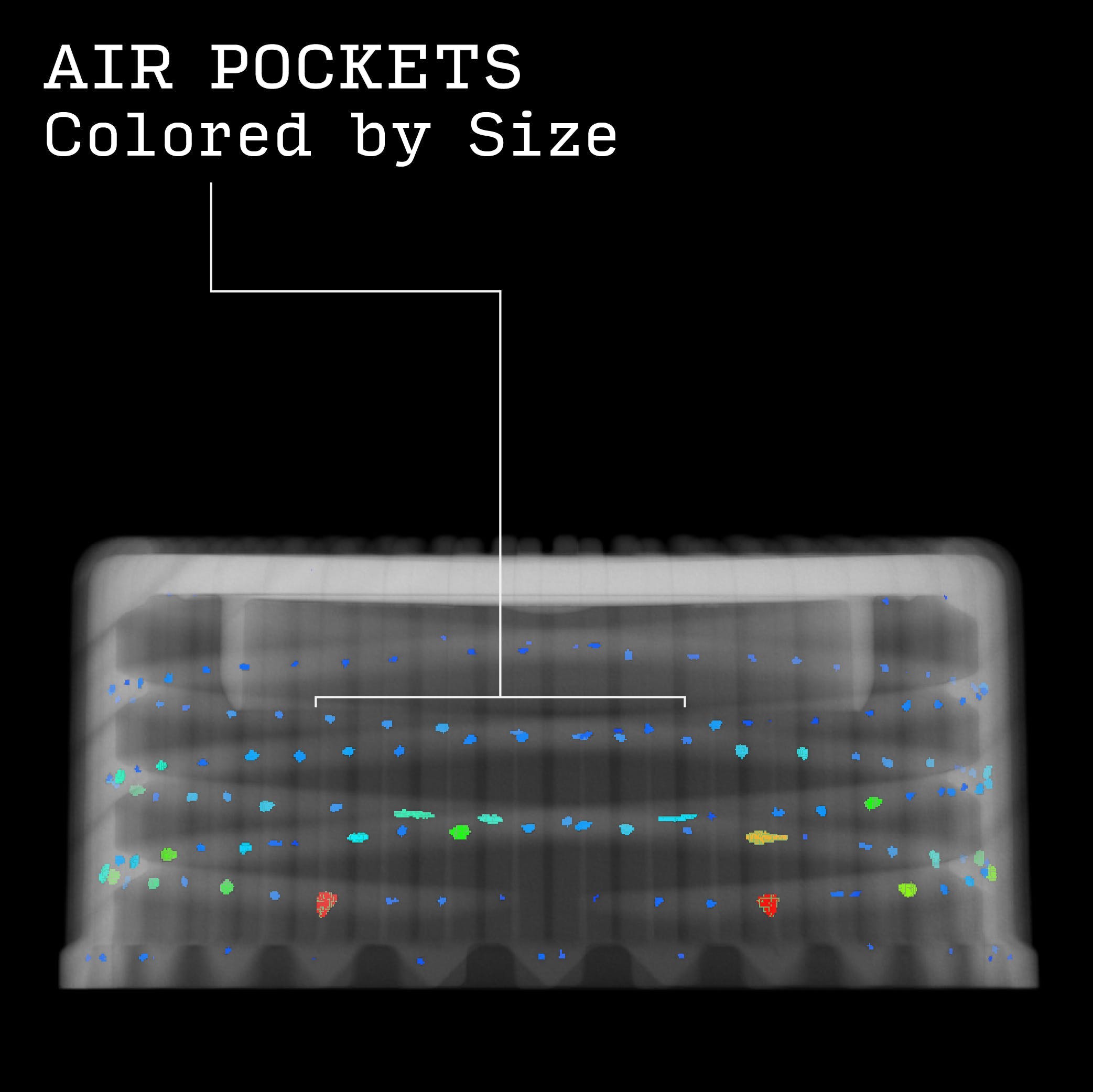
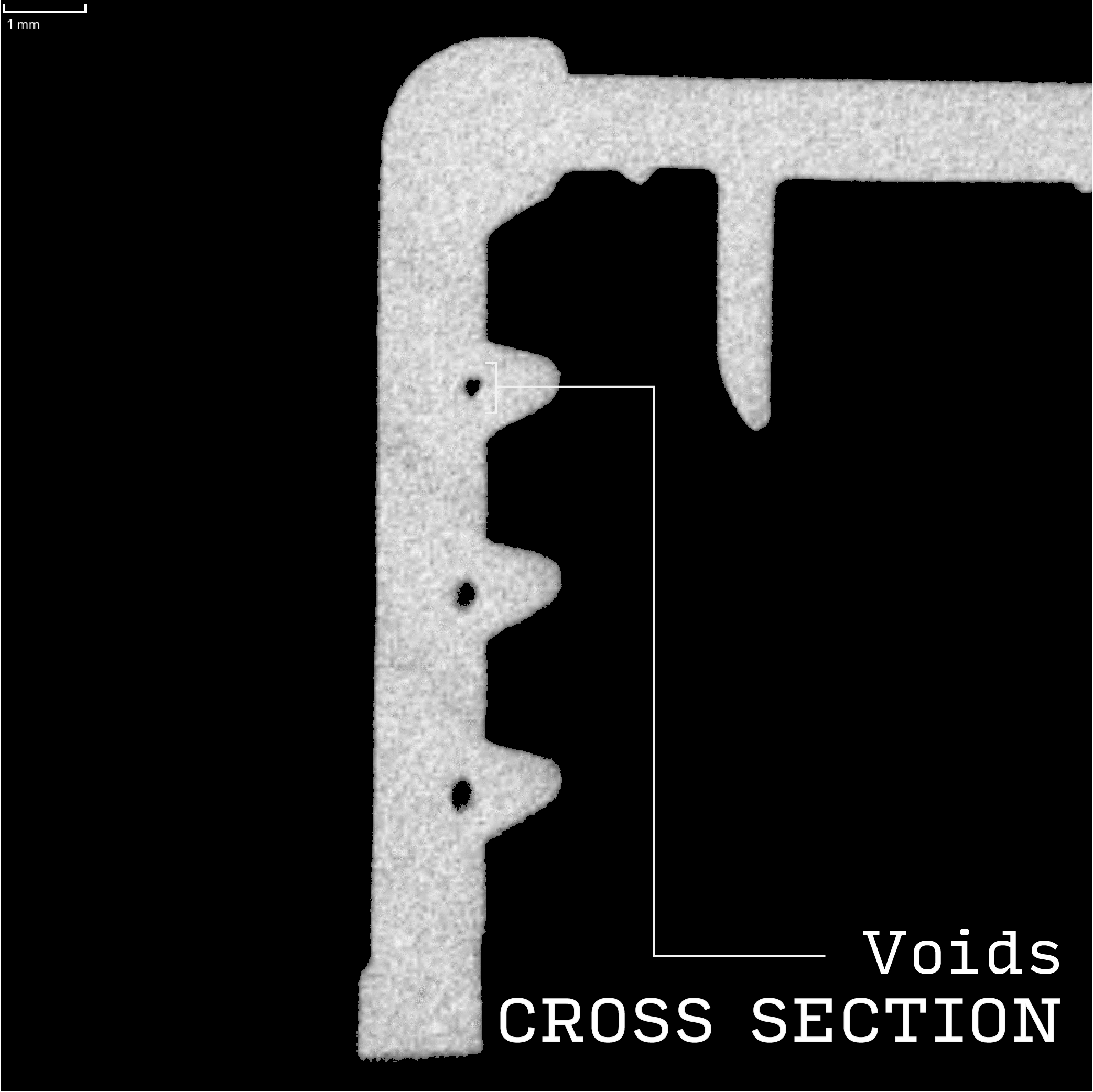
Revolving a slice plane in Lumafield’s Voyager software exposes hidden details inside the walls of the cap.
L'Oréal's Packaging Qualification Lab anticipates using Lumafield more frequently for proactive testing to improve the speed at which they can bring products to market. Looking into the future, Mahoney says, “I think we could set a standard during the conception phase, lock it in, and then have the production team reference that standard throughout the life cycle of the product.”