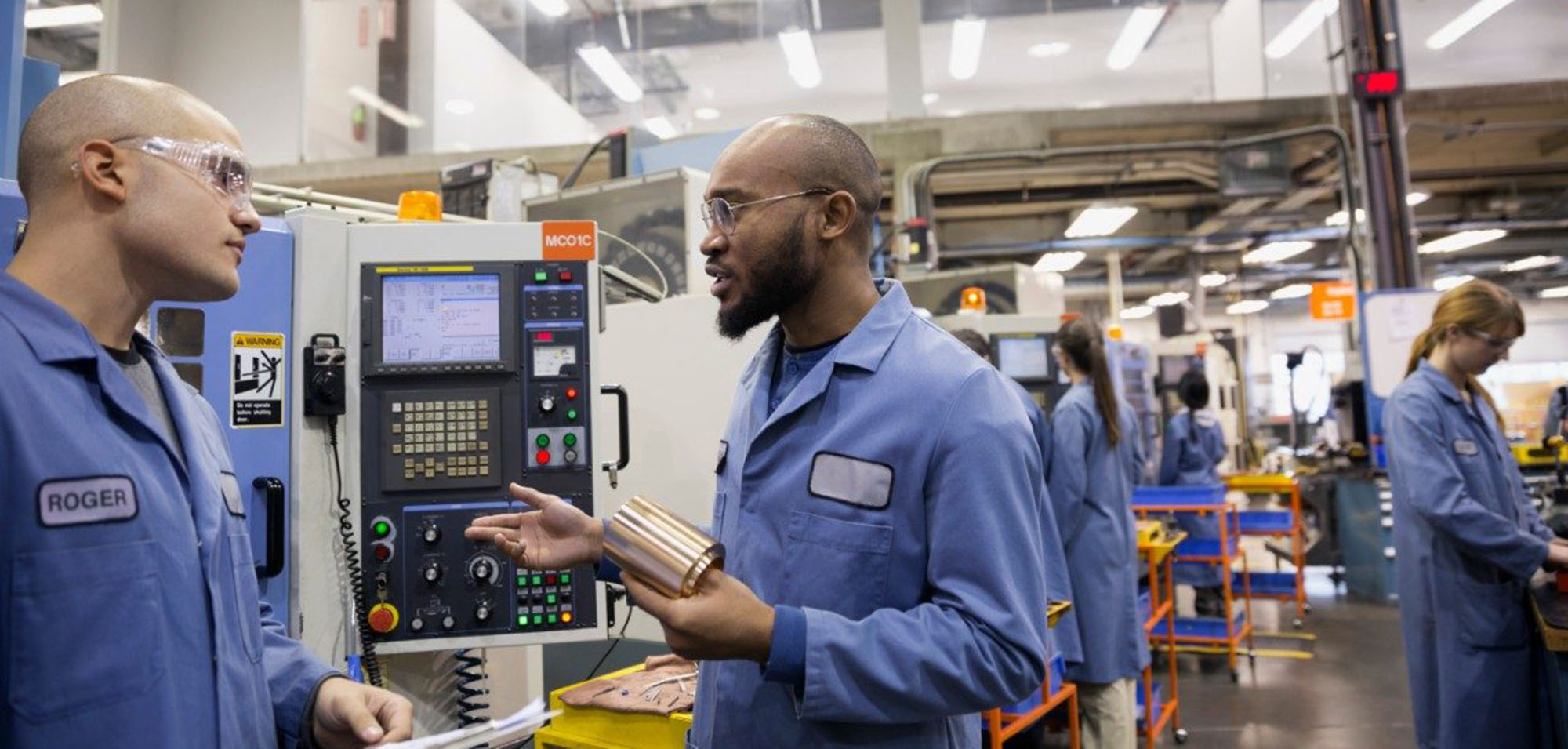
Eaton inspects critical parts 8x faster and achieves significant ROI with Lumafield’s industrial CT platform.
Summary
- Eaton has reduced inspection time from weeks to hours, saving over $90K on outsourced scanning in the first year of working with Lumafield.
- Eaton can slice, measure, and diagnose manufacturing anomalies by drawing on comprehensive CT data to achieve the highest level of quality assurance.
- Eaton is harnessing the versatility of Lumafield's intuitive platform for a wide array of uses, from driving material innovation to refining reverse engineering workflows.
- By integrating Lumafield’s microfocus CT and Triton systems, Eaton will be adding high-resolution component analysis and automated in-line inspection to their toolkit.
Background
Eaton’s products help the world manage increasingly complex electrical, hydraulic, and mechanical energy systems. As every industry transitions to greener forms of energy, Eaton is leading the way in developing power management solutions that are reliable, efficient, safe, and sustainable. But these solutions require novel engineering work and present challenges at every stage of the product development process, from R&D to mass manufacturing.
For Mechanical Engineer Kirstyn Hein, there was no time to lose when Eaton discovered an issue with a truck valve housing component that was holding up a multi-thousand vehicle assembly run. She knew immediately that the team needed to inspect a set of the components in question, and she had just the right tool for the job. Armed with Lumafield's Neptune industrial X-ray CT scanner, Hein quickly started scanning and soon identified the flaw—a subtle imperfection in material mixture. Using Voyager’s color mapping of attenuation values, Hein isolated the density differentials that were causing the component to break. After identifying affected batches, Hein remembers, “We saw which were good and which were bad, and we released the majority of the trucks that same day.”
With Lumafield’s CT scanner and software, the entire part can be inspected in much greater detail, reducing inspection time from 3-6 days to just 3 hours while keeping the product intact.
—Kirstyn Hein, Mechanical Engineer, Eaton
Accelerating innovation with non-destructive testing (NDT)
Eaton’s Vehicle Group, a premier tier 1 supplier to the world’s automotive manufacturers, is leveraging Lumafield’s inspection platform for far more than just failure analysis. Eaton’s products range from intricate micro-electrical components to robust power and hydraulics systems for both personal and commercial vehicles, and they frequently include complex matings of headers and terminals in electrical connectors.
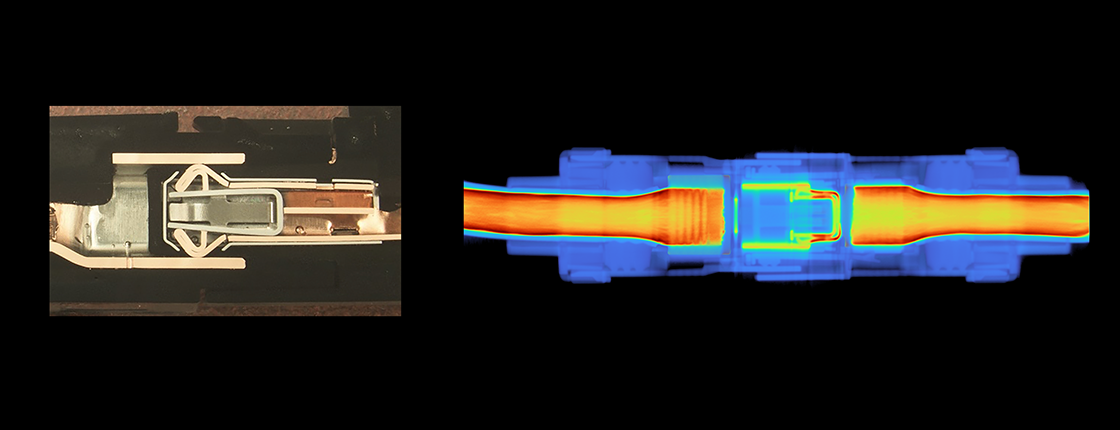
In the past, assessing these crucial junctures was a four-day ordeal that ultimately sacrificed the part for a single 2D glimpse of its internals. Now, with Lumafield's Neptune scanner and Voyager software, Eaton obtains insights 8x faster while keeping the part intact. Replacing manual cross-sectioning with non-destructive testing techniques such as industrial CT not only saves precious engineering hours and significant resources, it also yields richer data that allows for detailed analyses of both internal structures and external features. This comprehensive view is invaluable for defect identification, assembly verification, and root cause analysis.
At Eaton, Lumafield’s Neptune scanner and Voyager software allow us to find part mating issues 8x faster, and we also get a vastly more useful 3D model as opposed to the 2D image from before.
—Kirstyn Hein, Mechanical Engineer, Eaton
Ensuring material integrity for additive manufacturing
Additive manufacturing plays a crucial role as Eaton paves the way for the next generation of power management. Lumafield’s industrial CT platform serves a dual purpose in this effort: diagnosing common 3D printing issues such as trapped powder, closed channels, and internal voids; and aiding in the reverse engineering and material research process.
Lumafield’s platform is proving key to Eaton’s material research, particularly in the study of new waxes for investment casting. Voyager’s dimensioning tools allow Eaton engineers to fully quantify and account for the shrinkage of materials during cooling, guaranteeing the integrity of the final molds. “When we change a product design, Lumafield’s technology allows us to instantly see if the part is still doing its job.” Hein highlighted, “It’s hugely helpful.”
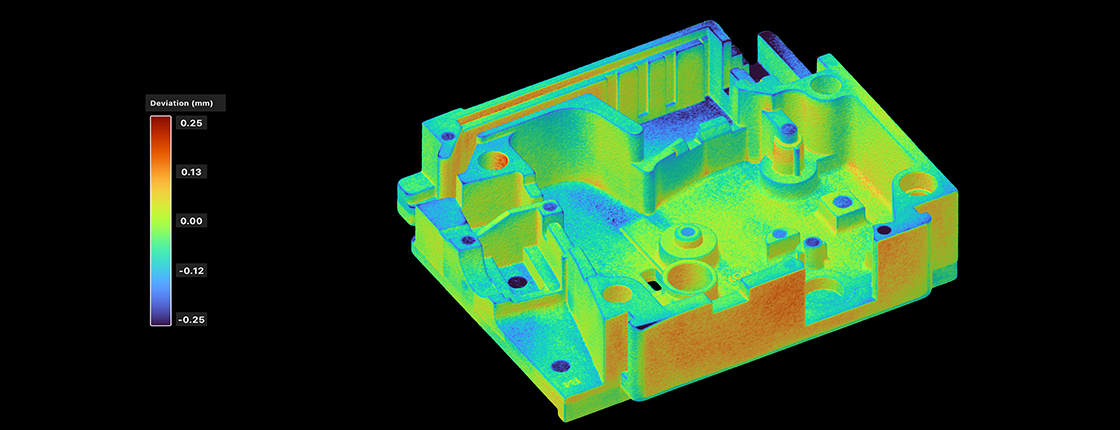
Joining forces with Germany’s Fraunhofer-Gesellschaft, the world’s leading applied research organization, Eaton’s Industrial Controls and Protection Division (ICPD) is scrutinizing injection-molded and 3D-printed automotive parts like fuel caps. Eaton is leveraging Lumafield’s Analysis Recipes tool to automate the measurement of internal porosity in injection-molded automotive components, accelerating analysis time by 4-6x. Voyager swiftly detects, quantifies, and visualizes deviations above a customized threshold; and Atlas, Voyager’s built-in AI co-pilot, can draw on its encyclopedic manufacturing knowledge to offer guidance for taking corrective measures.
With Lumafield, we get a fast reconstruction that shows porosity without slicing, potting, or using calipers, and we can instantly see the problem.
—Kirstyn Hein, Mechanical Engineer, Eaton
Overcoming supply chain disruption with reverse engineering
Eaton also recently faced the challenge of producing a complex polymer part in-house, made more difficult by the absence of an original CAD file. 3D optical scanners proved inadequate because they could not capture the full geometry of the part’s intricate internal passageways. Lumafield's CT platform, however, offers a simple workflow for reverse engineering a new CAD model from an existing part.
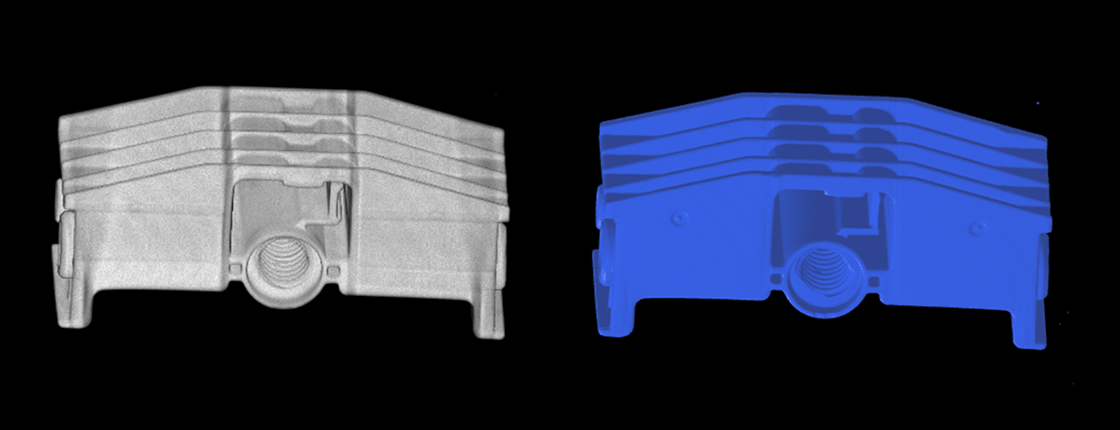
Unlike surface scanners that can only capture external contours, CT scanning penetrates the entire volume of the part, allowing for the accurate capture of internal geometry and features hidden by overhangs and crevices—details essential for the part’s functionality and manufacturability. Industrial CT ensures that even completely concealed elements are rendered in high fidelity. Voyager allows for mesh export to CAD software, where the design can be refined and then produced in-house. During periods of supply chain disruption, Lumafield’s reverse engineering workflow makes Neptune and Voyager indispensable tools in Eaton’s arsenal.
Unlocking collaboration between distributed teams
Hein also directs an internal scan bureau from Eaton Research Labs in Michigan, providing a user-friendly inspection technique with unmatched turnaround speed to her colleagues in all of Eaton’s business units. “Eaton loves to invite partners to view and interact with Lumafield’s scans,” Hein says. “With browser-based Voyager, it’s as easy as sharing a link. Collaborators can open the scan on their own computer, make bookmarks, and leave comments for their colleagues.
Voyager helps Eaton streamline product development and production across international business units through one collaborative software platform to share, review, and edit scans in real time.
—Kirstyn Hein, Mechanical Engineer, Eaton
Positive ROI within a year
Overcoming bottlenecks in product development, Eaton conducts inspections at unprecedented speeds, condensing weeks of work into a few hours, as they continually discover new applications for the scanner across their operations. These time savings also have significant financial implications, freeing up both engineers’ time and resources to allow them to focus on creating the sustainable energy solutions that matter most to them.
Lumafield’s technology is easy to use, and the ROI has been phenomenal. We saved $90K in our first year. It blows competitors out of the water.
—Kirstyn Hein, Mechanical Engineer, Eaton
Expanding Lumafield and Eaton’s partnership
For Hein and her colleagues, the relationship that they have built with their Lumafield support team is just as valuable as the technology itself. “Everyone at Lumafield has that ‘It’ factor,” Hein notes, adding “We have never had this positive of a relationship with an outside company.” With a Lumafield Account Executive and Solutions Engineer nearby in Michigan and ready to support Eaton’s inspection needs with regular in-person visits, Hein is looking forward to what the future holds.
Lumfield develops its solutions in response to the inspection needs of its customers. Eaton is deepening this partnership by adding Lumafield’s newest systems to their toolkit. These include a High Resolution Neptune, which will crisply capture fine features, particularly of electronic components. Lumafield’s high-throughput Triton system will integrate into Eaton’s production facilities with automated in-line and line-adjacent inspection, to ensure quality at scale.
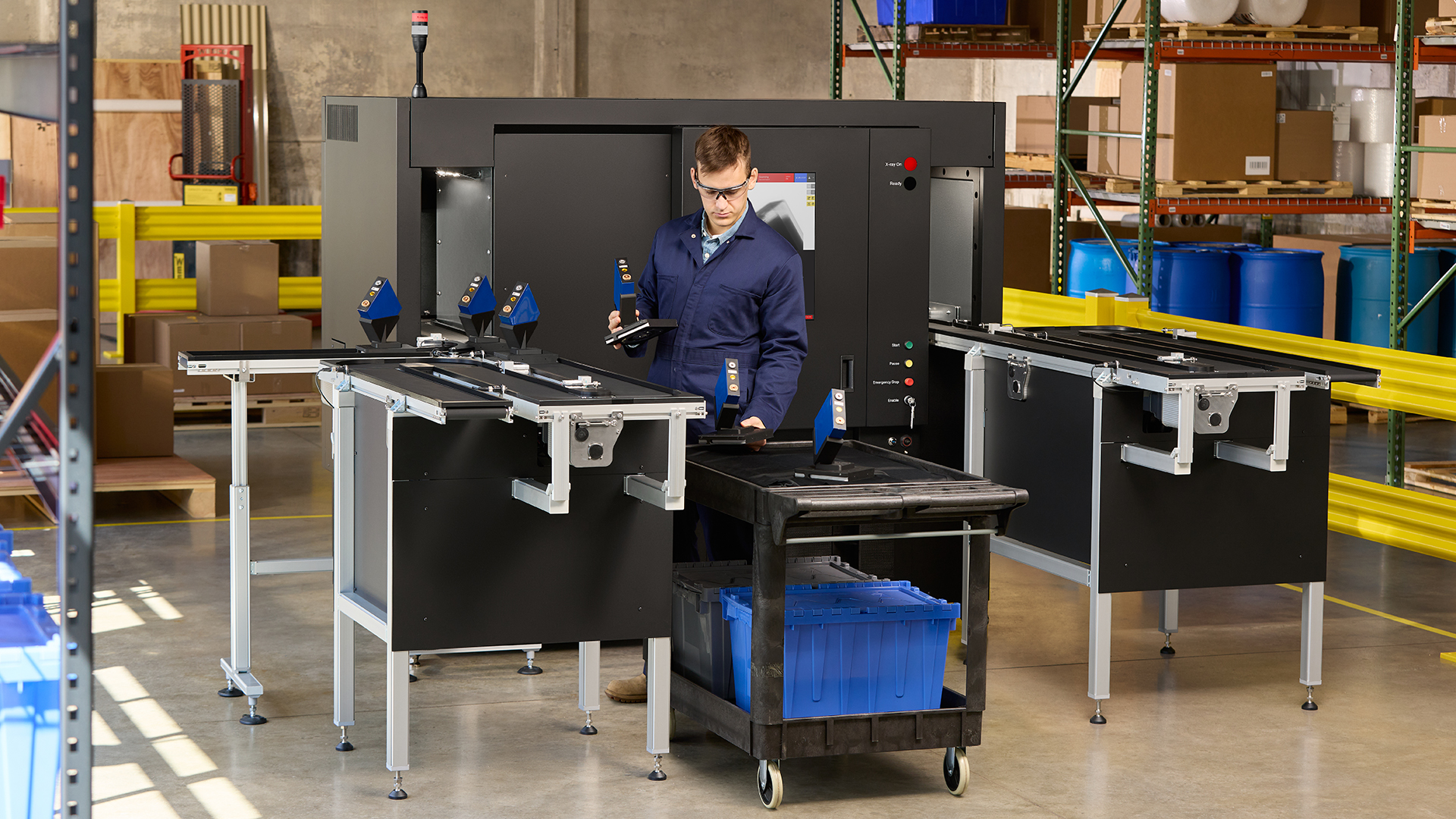
Eaton's proactive expansion of their Lumafield technology suite signals a commitment to maintaining their edge in power management innovation. By harnessing the most advanced hardware and software solutions, Eaton is not only redefining their own production standards but also setting a benchmark for the entire industry.