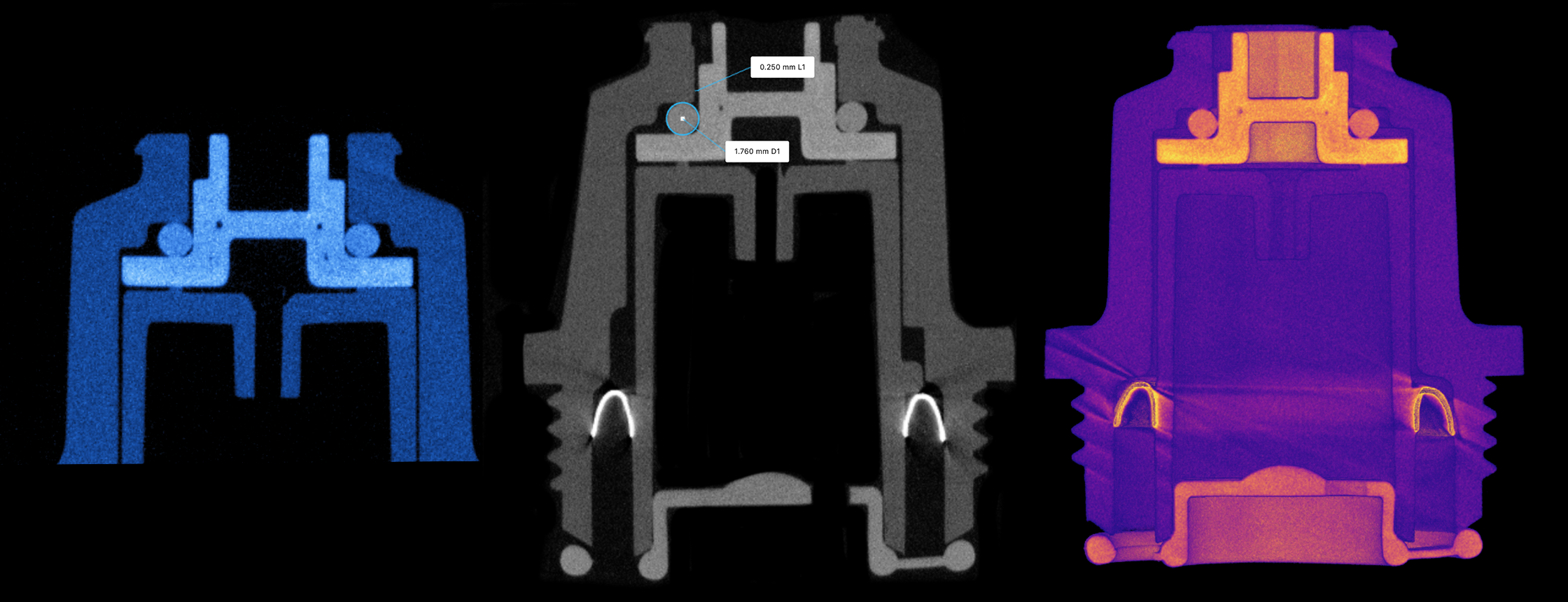
A global automotive supplier streamlined the Design Verification and Production Validation (DV/PV) process.
Summary
- After moving from traditional destructive testing methods to Lumafield's industrial CT inspection platform, a global automotive supplier improved operational efficiency and bottom-line results.
- The Neptune scanner and Voyager analysis software streamlined the Design Verification and Production Validation (DV/PV) process, reducing reliance on costly and time-consuming methods.
- Comprehensive, non-destructive insights into a component that had become warped during manufacturing accelerated problem identification and resolution.
- Lumafield's technology is fostering innovation, enhancing OEM relationships, and ultimately delivering a powerful competitive advantage within the industry.
Background
Our customer is a large automotive supplier known for producing seating and electrical systems for many of the most recognizable original equipment manufacturers (OEM) in the automotive industry. As a result of the rigorous quality control standards and accelerated production timelines maintained by these OEMs, suppliers often run very lean and have to be highly cost sensitive. Even with over $23B in annual revenues and nearly 175K employees worldwide, this customer is no different; even the smallest improvement to their inspection processes can provide a significant operational benefit.
With the average lifespan of a car now expected to be 12 years and upwards of 200K miles, each of the tens of thousands of components that make up the vehicle must be capable of performing perfectly over a decade of stress and use. The slightest defect or internal failure can have devastating consequences for both passengers in the vehicle and the manufacturer. Suppliers and OEMs must maintain uncompromising quality control standards as they develop the individual components in each vehicle.
Traditional testing methods in the automotive industry have historically been both inefficient and imprecise. Suppliers have relied heavily on destructive testing in the component inspection process for decades, but more stringent engineering safety margins and higher product quality standards in the industry now necessitate a more innovative solution. With that in mind, engineers at this company sought a tool that would provide more comprehensive insights into their components than traditional testing methods.
Comprehensive DV/PV Testing
Industrial CT technology was the clear solution for the customer’s engineering team. CT scanning is an unparalleled tool for non-destructive testing of automotive components of all materials and densities, and Lumafield’s Neptune industrial CT scanner quickly transformed the company’s testing processes.
Overhauling Design Verification and Production Validation (DV/PV) testing was a key factor in the company’s decision to adopt Lumafield’s Neptune scanner. DV/PV testing ensures that suppliers meet the rigorous design standards maintained by OEMs and validates that the manufacturing process can consistently produce parts that meet all quality and performance standards. Before implementing CT scanning, the company’s DV/PV testing was an inefficient process due in part to its reliance on wasteful destructive testing that often uncovered defects late in the production cycle.
Our Neptune scanner pays for itself tenfold in streamlined DV/PV testing alone. Having the ability to show OEMs exactly how our parts meet their specs during production builds trust and speeds up the whole process.
— VP of Engineering
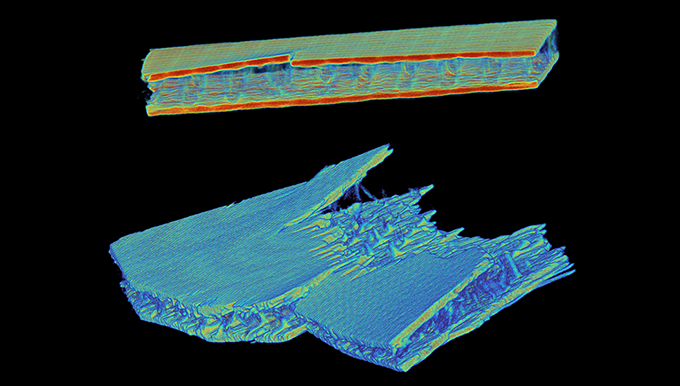
With the addition of a Neptune scanner in-house, the company now has access to highly sophisticated inspection data through every phase of the engineering cycle. This proved especially valuable when engineers noticed that prototypes of a newly developed dashboard component constructed with resin were experiencing warping, which caused the measurement of the component’s diameter to deviate from specifications. Within a matter of hours, Voyager’s CAD Comparison tool allowed the team to evaluate how the prototypes had diverged from the original design and empowered the engineers with the information they needed to fine-tune the manufacturing parameters.
There’s something about actually seeing inside a part that unlocks a whole different level of understanding. Voyager doesn’t just give us simple scan data, it gives us the insight we need to innovate faster with the confidence that we’re delivering top-quality parts.
— VP of Engineering